It was about 40…
Years ago, whilst sitting in a chair at the local tailors, I asked my father the question – why should you wear a custom made suit, Dad? The response was a long one, but the thing that stuck in my mind was the look of sheer pleasure on my father’s face. This wasn’t when the tailor was taking his inside leg measurement, by the way. Now you might be thinking, “what’s all this got to do with cabinet making?” Well, rather a lot really as the process is not that dissimilar, bespoke tailoring is all about the process, quality of materials and attention-to-detail, the superiority of the fabric, the cut of the cloth and the craftsmanship required for the final stitched garment. If you had the option, why would you settle for something off-the-rack when you can indulge in a spot of sartorial elegance.
The same is true of custom furniture making. It’s about the journey, the creation of a piece, hand-picked materials, and the choice of finishes; as is the case with bespoke tailoring, it certainly isn’t ‘one size fits all.’
The beginning
The starting point with custom furniture making is about the relationship between furniture designer and client. The focus is on the end-user’s preference over the materiality, the features and function, and the construction methods employed. More generally, bespoke cabinet making includes a high degree of customization and involvement of the end-user in the production process with their request and lifestyle in mind. Like all Groth & Sons projects, the consultative stage is essential. Time and care are given long before production begins. This design process commences with the client brief, determining the furniture requirements, and the designer addresses the technical and aesthetic elements.
Furniture requirements
Above all else, a piece of furniture should perform the functions asked of it. It should be sufficiently strong and sturdy enough for its requirements and designed to tolerate any movement in the materials which will inevitably occur due to changes in humidity, particularly with the Sydney climate in mind. The construction should be within the craftsman’s aptitude, and it should be pleasing to the eye. Therefore, with these criteria in mind, there are two primary considerations when crafting a piece of furniture; the one technical and the other aesthetic, the relative importance being dependent on the intended purpose.
Technical elements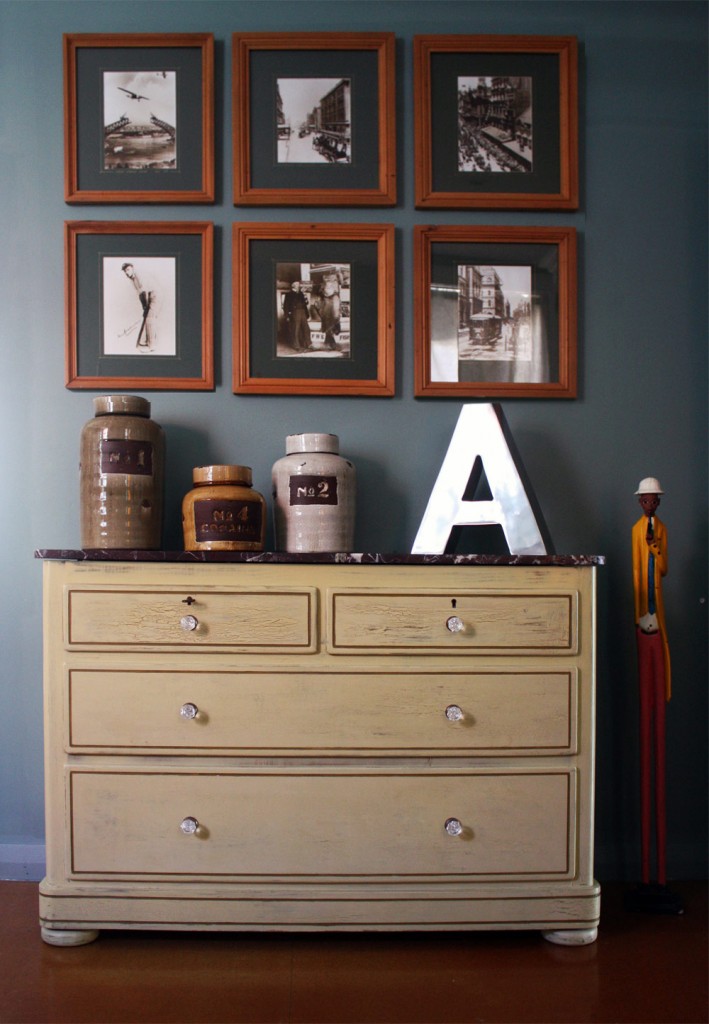
Common sense prevailing, the suitability of function should be a starting point in the design and construction phase of furniture making. For example, a library bookcase has to fit the intended space satisfactorily and accommodate a series of books and objects. Consequently, allowance must be made in terms of height and depth, but also in terms of weight. One should consider the relationship between span and stiffness to prevent sagging. There should also be sufficient tolerance allowed for the natural movement of the wood. Thought must also be given to the installation into the environment regarding the modular aspect of the piece. It is most necessary for a larger furniture item to be dismountable for ease of transport and delivery.
Aesthetic elements
Considering the elements and principles of design, it is possible to decide how the final result will look in terms of scale, balance, proportion, etc. It is important to consider the building’s surroundings as well. Is it a contemporary building, or is it a heritage site? Will the piece fit into the building’s design aesthetic, or are you looking for a contrast of details? The project may be concept-driven and unexpected, whimsical, or even treated as an art installation in its own right. Whatever the appearance, there must be a consideration for the balance between visual appeal and functionality, and the designer must be on guard against subverting the practicality of the piece.
Intrinsic value
Custom made furniture sets the tone of an interior and can accommodate your prerequisites. You may have to wait longer, and the price tag may not resemble that of its foreign made-assembly-line-counterpart. Still, with consideration to design development, something beautiful will emerge. Groth & Sons specialize in producing one-off pieces of furniture that incorporate the use of contemporary construction methods with a traditional aesthetic. From drawing board to delivery, crafting detailed hand-finished projects exuding the artisan’s passion and expertise. These handcrafted pieces of today are the heirlooms of tomorrow.
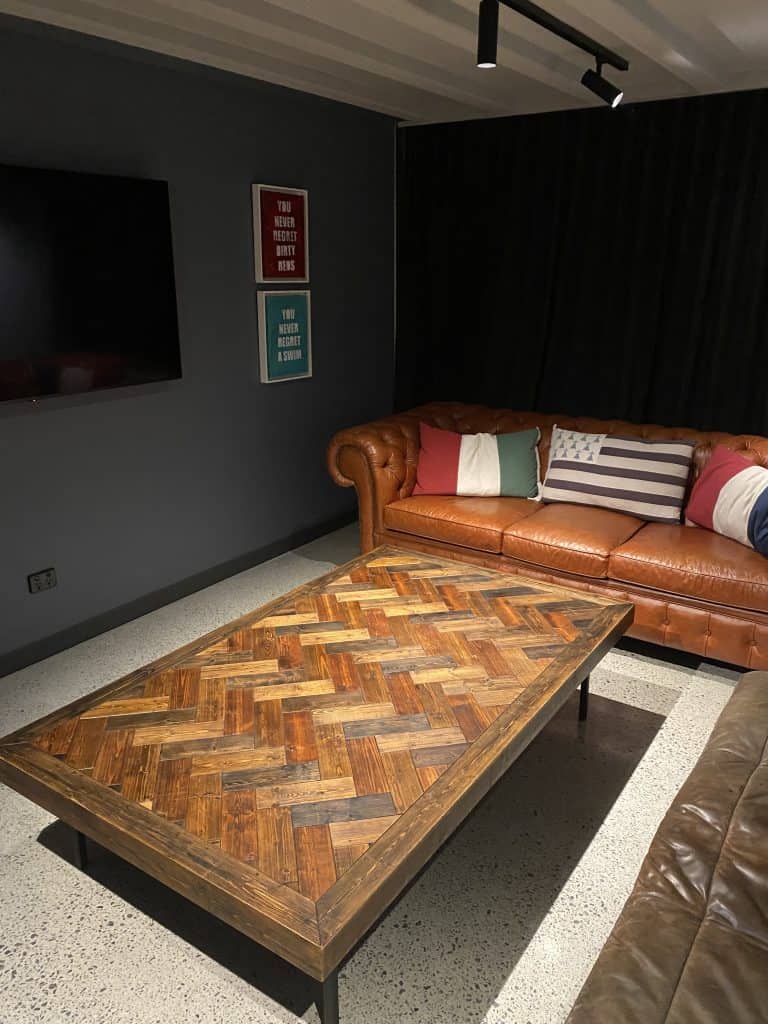
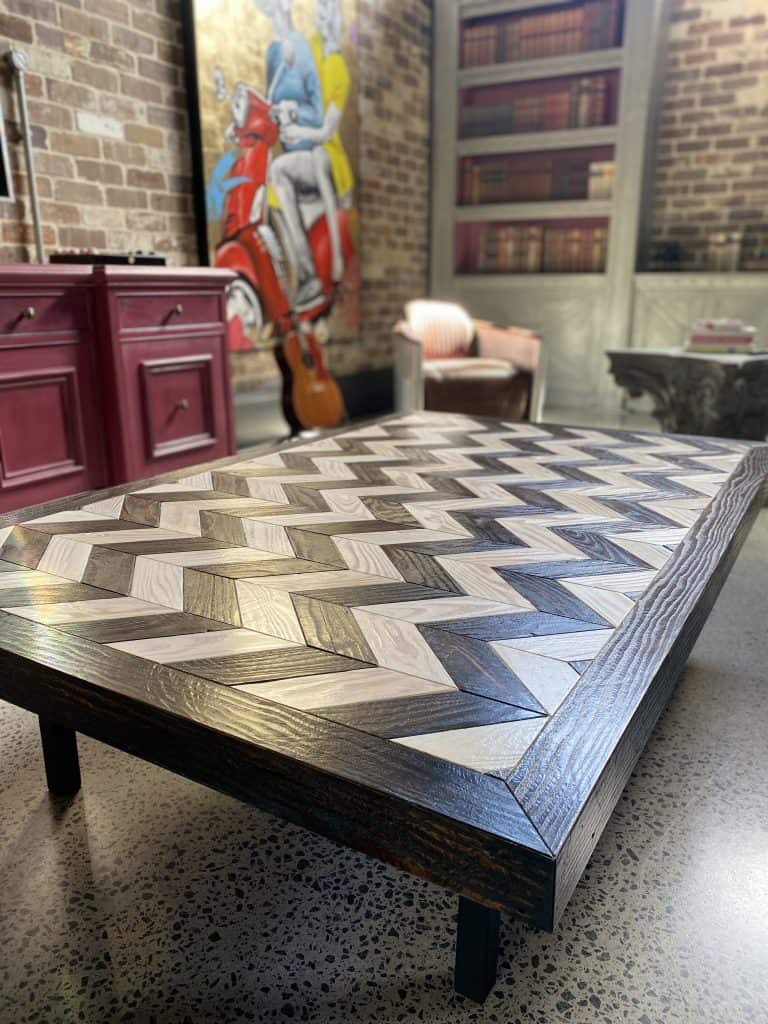
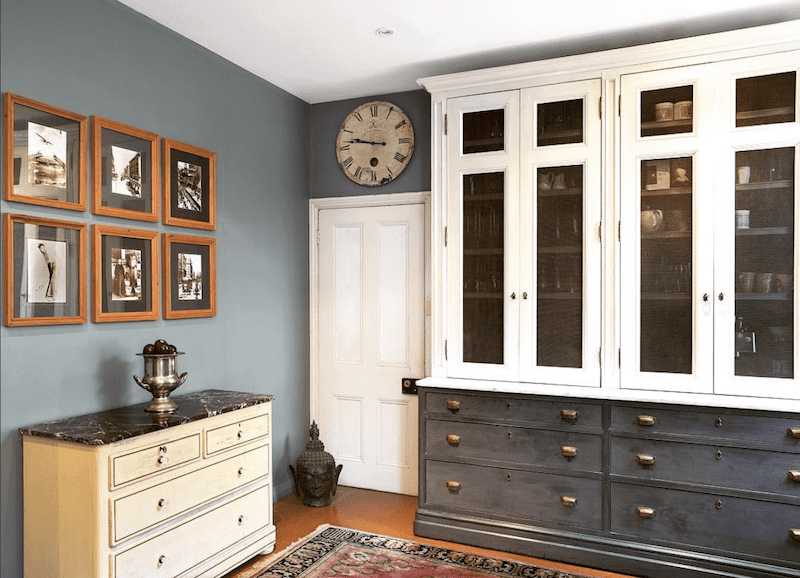
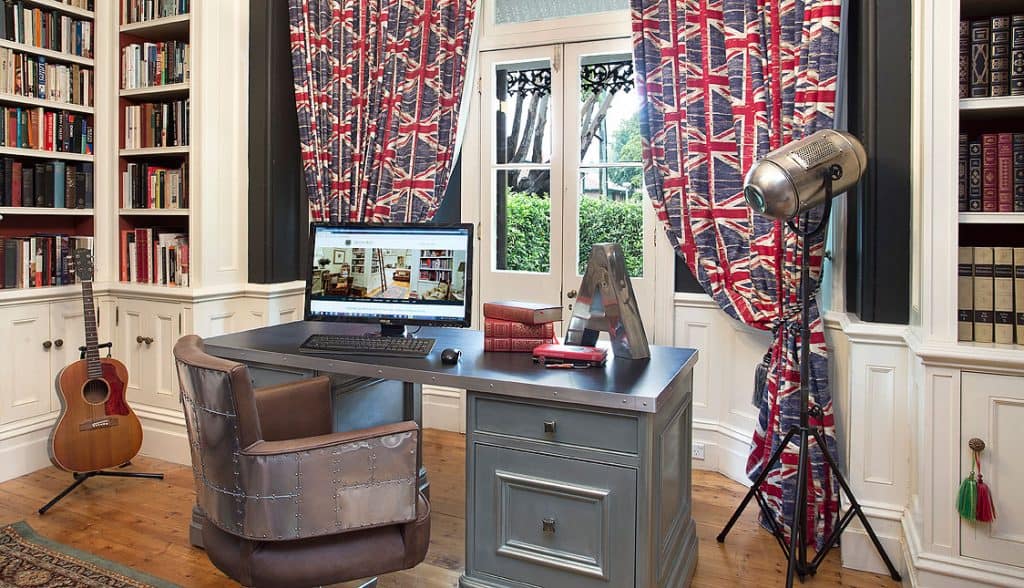